翻边
- Flanging;turnup;purfle;revers
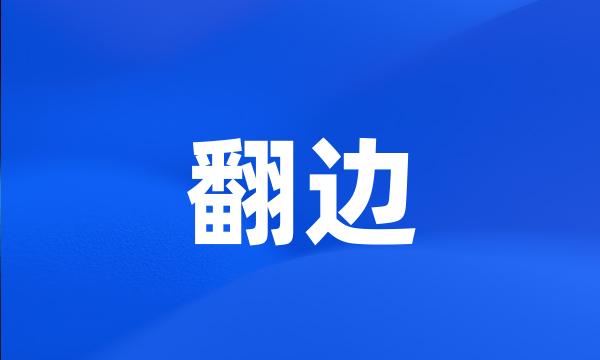
-
汽车消声器筒体翻边工艺及模具设计汽车消声器筒体翻边加工过程的数值模拟
Barrel Purfle Manufacturing and Mould Design of Automobile Noise Silencer Numerical Simulation of Extrusion Process for Moter Silencer Tubes
-
F型强火力燃气灶面板成形、翻边工艺及其模具
Forming , flanging and die for panel in F type gas kitchen with strong fire
-
在理论研究的基础上,作者开发了垂直翻边类模具结构设计CAD软件,包括凸模、凹模镶块、顶出器、加强筋布置、功能组件调用等设计模块。
A CAD system for vertical flanging dies structure design has been developed on the basis of theoretical study .
-
基于神经网络和有限元法的V型件翻边成形性能研究
Research on Flanging of V-Shaped Sheet Metal Part Based on Artificial Neural Network and Finite Element Method
-
根据翻边工艺计算翻边系数K,计算分析拉深次数。
The flanging coefficient K was calculated according to the flanging process . Drawing times was analyzed and calculated .
-
基于薄板翻边回弹试验的RBF神经网络模型
Modelling of Springback with RBF Neural Network Based on Experiments in Flanging Operation
-
V型件翻边成形的数值模拟面向样件的二维钣金件优化排样方法研究
Numerical Study on Flanging of V-Shaped Sheet Metal Part A Part - oriented Method of 2D Sheet Metal Nesting
-
把人工神经网络(ANN)和遗传算法(GA)相结合进行工艺优化设计,研究了S形件翻边成形中的工艺参数优化。
Technological parameter optimization design was researched by combining ANN and GA in forming S-shaped pieces .
-
有限元仿真与人工智能相结合的BP人工神经网络模型可以快速有效地预测翻边成形性。
The BP neural network model based on finite element simulation and AI technology can quickly and effectively predict the flanging formability .
-
采用弹塑性大变形有限元方法研究了几何形状和材料参数对“V”型零件翻边的影响;
A large deformation elastic plastic FEM model is employed to simulate the stretch flanging of V shaped sheet metal parts .
-
针对U形件中多角对回弹的影响,设计了一组带翻边、不同弯角数的U形件进行实际冲压成形试验。
A series of flanged and multi-angle U shaped parts were designed in allusion to influences on springback by multi-angle to conduct punching experiments .
-
结果表明,几何形状,尤其是零件张角,对V型零件翻边成形性具有决定性的影响。
The results show that the geometry , especially the flange angle , is a key factor to the formability on flanging of V-shaped sheet metal parts .
-
本文将有限元模拟与人工智能相结合,建立了基于改进的BP神经网络的“V”型件翻边成形性能与几何尺寸及材料参数关系的数学模型。
Based on the integration of ameliorated BP neural network and finite element method , a model for prediction of the flanging of V shaped sheet metal parts was presented .
-
这种方法把图形软件和高级语言逻辑结合,大大简化了镶块模CAD系统设计中的图形输入。翻边凹模镶块交接型式的分析
This way , which connect advanced computer language with software for picture , simples inputting picture in CAD system of sectional die design greatly . Analysis of Joint Type of Flanging Die Insert
-
基于DYNAFORM的圆孔翻边数值模拟研究
Numerical Simulation Research for Hole-flanging Based on DYNAFORM Software
-
基于此模型,研究了零件张角、翻边部分初始长度以及材料各向异性参数和应变硬化指数对V型零件翻边的影响。
Based on the model , effects of flange angle , initial flange length , strain hardening exponent and normal anisotropy coefficient on the flanging of V-shaped part were unveiled from the calculated result .
-
圆孔翻边的数值模拟基于ABAQUS软件,对圆孔翻边成形过程进行了模拟分析。
Numerical simulation of hole flangingBased on ABAQUS software , forming process of hole flanging is simulated .
-
本文重点开展了凸弧翻边、凹弧翻边、V型件冲压、U型件冲压等典型冲压工序的回弹试验研究。
This paper emphases on experimental investigations on springback in typical forming operations such as convex edge flanging , concave edge flanging , " U " shape component forming , and " V " shape component forming .
-
首先从CAD与CAE的集成技术、SolidWorks二次开发、修边和翻边成形工艺以及采用的有限元基本理论等方面深入研究了系统的开发基础。
Firstly , the development foundation of the system was deeply studied , based on integration of CAD and CAE , redevelopment of SolidWorks , trimming and flanging process and basic theory of FEM .
-
12×4J轮辐翻边变形分析及工艺改进
Strain analysis of 12 × 4J wheel burring process and improvement of technology
-
TA2Mδ2.0钛合金外缘翻边成形过程中的形状畸变现象
Shape Distortion in Curve Flanging Forming Process with TA2M δ 2.0 Titanium Alloy Sheets
-
本文研究了罐身马口铁激光焊接工艺和焊接参数对焊接速度和质量的影响,检验了焊接接头的组织和性能,分析了Sn在焊缝中的分布,并进行了空罐的翻边试验。
The authors studied the welding technology and parameters for the tin-plate can and thier influence on welding speed and quality , investigated the microstructure and properties of the weld , analysed the distribution of tin in weld metal and carried out the flange test of the can body .
-
随后用eta-Dynaform软件在三维状态下分析了压边力、摩擦系数和材料对翻边回弹的影响,并得到了这些因素对翻边回弹影响的基本规律。
Then the binder force , friction coefficient and material , and their effection on springback were studied by using eta-Dynaform in 3D state .
-
该模型不仅能考虑厚向(平均)异性系数,而且也能考虑R0、R45和R90厚向异性系数对翻边高度的影响。
Not only the influence of average normal anisotropic coefficient but also the one of R 0 、 R 45 and R 90 on the flanging height can be considered in this model .
-
结合具体算例,用ADINA软件模拟了变形区的应力、应变及模具上的受力,得出了与理论分析相同的结论,即翻边使变形区变薄;
Using concrete calculated example , the stress , strain and the mold stress are simulated with ADINA software . It is shown that the simulation results of the stress strain change rule along with the die angle are in good accordance with that of the main stress method .
-
对车轮内孔翻边极限翻边因数的主要影响因素做了讨论,在此基础上,对12×4J车轮轮辐中心孔翻边模翻边进行了工艺计算。
The turring parameter of turring model of wheel inner hole is discussed in this paper , on th basis of this , the technology calculation of 12 × 4J wheel hole turring process is carried on in this paper .
-
中通道冲压件成形方案为拉延-修边冲孔-翻边整形,模拟结果验证了该方案的可行性,中通道冲压件成形缺陷基本消除;3、基于AUTOFORM软件对中通道进行全工序回弹模拟。
The middle channel stamping program was drawing-trimming and punching-flanging and shaping . The simulation results demonstrated the feasibility of the program , and the forming defects were basically eliminated . 3 . Springback simulation of the whole forming process of the middle channel based on the AUTOFORM software .
-
内孔翻边时变形区应力应变规律研究
Stress strain rule studies of deformation area of inside hole flange
-
车轮轮辐中心孔翻边模具设计
Design of burring die of center hole of the wheel disc
-
在压力机一次行程中冲孔、翻边和增厚边缘
Punching , Flanging and Thickening on One Stoke of Press Machine